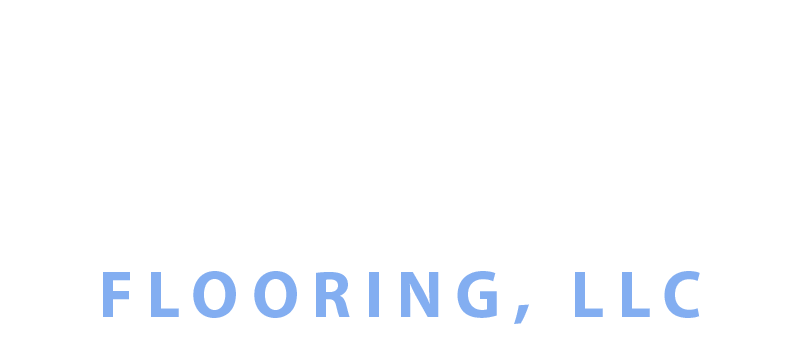
Laura Gibson
December 4, 2024
Table of Contents
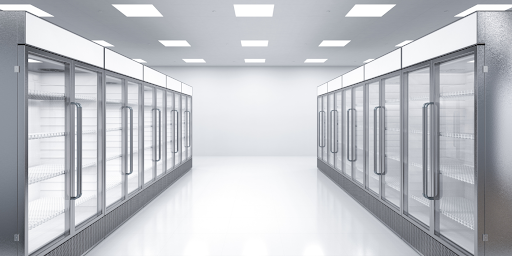
In home renovation, solid epoxy floors can significantly influence both aesthetics and functionality. Traditionally, homeowners have leaned towards options like hardwood, tile, and carpet. However, a notable shift has been occurring, with solid epoxy flooring emerging as a robust contender. Epoxy is progressively favored for its modern appeal and long-term cost-effectiveness.
This article provides an extensive comparison of solid epoxy floors with traditional flooring solutions. We aim to equip you with detailed insights to make an informed decision on the best flooring for your home. Continue reading to explore which option offers the long-term value.
What is Solid Epoxy Flooring?
Solid epoxy flooring is a specialized type of floor coating that combines resilience and aesthetic appeal. This flooring solution is crafted from epoxy, a polymer that hardens upon curing, providing a durable and seamless finish. Predominantly used in commercial and industrial settings, solid epoxy flooring is also gaining traction in residential spaces due to its robust characteristics.
It is characterized by its efficient installation process and the singular, uniform color that spans the entire surface. Despite the name “solid color,” property owners can select from a broad spectrum of colors, allowing customization to fit any décor or branding requirements.
Suggested Reading: Breaking Down The Molecular Structures of Epoxy and Polyurethane for Better Choices
Benefits of Epoxy Flooring
- Durability: Epoxy floors are popular for their strength and are resistant to wear. This makes them suitable for areas with heavy foot traffic and heavy machines or equipment.
- Ease of Maintenance: The seamless nature of the durable floor prevents the accumulation of stubborn dirt and debris, making it easy to clean. A simple sweep and mop are all it takes to keep the floor looking shiny.
- Aesthetic Versatility: Available in a wide range of colors, epoxy flooring can be tailored to suit any aesthetic preferences or functional needs.
- Chemical Resistance: Epoxy floors can withstand exposure to various harsh chemicals, which is ideal for warehouses or manufacturing plants.
- Safety Features: Options to add anti-slip epoxy coatings or reflectivity enhance safety by reducing slip hazards and improving visibility.
This overview should help clarify what solid epoxy flooring is and why it might be the right choice for various flooring needs, blending practical benefits with aesthetic flexibility.
The Cost of Installing Solid Epoxy Flooring
Installing solid epoxy flooring is an excellent choice for residential and commercial properties. This epoxy type of flooring involves applying a thick coating of epoxy resin over a concrete substrate, which, after curing, creates a smooth surface.
The average cost of installing solid epoxy flooring can vary widely depending on several factors. Primarily, the size of the area to be covered plays a significant role in determining the overall expense. On average, homeowners and business owners can expect to pay between $3 and $12 per square foot. This price range includes both epoxy flooring materials and labor costs for professional installation:
Material Cost
Materials account for a large portion of the expenses. High-quality epoxy resin costs between $30 and $150 per gallon, enough to cover approximately 100 to 150 square feet. The type of epoxy used—whether water-based epoxy, solvent-based, or 100% solids—also affects the cost, with 100% solids being the most expensive but also the most durable and long-lasting.
Labor Cost
Labor costs are influenced by the condition of the existing floor, the complexity of the job, and the geographic location. Floors that require extensive preparation, such as crack repair or leveling, will increase the total cost. Professional installers usually charge by the square foot or by the hour, with rates ranging from $1 to $7 per square foot or $30 to $80 per hour.
Special Features
There are other potential expenses, such as decorative flake finishes and textured surfaces. Some contractors may charge extra for moving furniture or fixtures and for the disposal of previous flooring materials.
While the initial investment in solid epoxy flooring installation might seem high, its longevity and minimal upkeep requirements make it a cost-effective choice in the long run. This flooring solution not only offers a visually appealing floor finish. It is also a highly resistant surface to stains, abrasions, and chemicals, making it a practical investment for many.
Longevity and Durability: Epoxy vs. Traditional Flooring
When comparing the longevity and durability of epoxy flooring to traditional flooring options like hardwood, tile, or carpet, several distinct advantages emerge in favor of epoxy.
Epoxy Flooring: Epoxy is renowned for its resilience and robustness. This synthetic flooring material is made from a mixture of resins and hardeners, which chemically bond to create a rigid plastic surface. This composition not only makes epoxy waterproof but also resistant to wear and tear from heavy traffic and industrial load. Epoxy floors can last anywhere from 10 to 20 years if properly maintained, depending on the volume of traffic and the environment in which they are installed. They are also resistant to stains, grease, and chemicals, making them ideal for garages, warehouses, and industrial settings.
Traditional Flooring: Traditional materials, while popular for their aesthetic appeal, have varying degrees of durability:
- Hardwood floors are susceptible to scratches, dents, and water damage. With diligent care, they can last for decades, but they often require refinishing every 10 years or so to maintain their visual appearance.
- Tile is durable and water-resistant, making it a popular choice for areas with moisture, like bathrooms and kitchens. However, tiles can crack under impact, and the grout may need to be replaced over time to prevent moisture and mold buildup.
- Carpet is comfortable underfoot and offers a variety of textures and colors. However, it is prone to staining and can accumulate allergens, requiring regular deep cleaning. Carpets typically need to be replaced every 5 to 15 years, depending on traffic and quality.
In environments where longevity and minimal maintenance are priorities, epoxy flooring often outshines traditional options. Its ability to withstand harsh conditions without frequent repairs or replacements offers a significant long-term expense advantage. However, for residential spaces where comfort and aesthetics are more crucial, traditional materials like wood or carpet might be preferred despite their higher maintenance needs.
Suggested Reading: Why Retail Giants Like Walmart Choose Commercial Epoxy Flooring?
Maintenance Costs: Epoxy Flooring vs. Hardwood and Carpet
When considering the financial aspects of flooring choices, it’s important to explore the initial installation costs and the ongoing maintenance expenses associated with epoxy flooring, hardwood, and carpet. Here’s a more detailed breakdown:
Epoxy Flooring
The initial installation cost of epoxy flooring ranges from $3 to $12 per square foot, depending on the complexity of the design and the condition of the underlying floor. This makes it a moderately priced option initially.
In terms of maintenance, epoxy flooring is very cost-effective, generally requiring only routine cleaning with no expensive cleaning supplies or professional services. The durability of epoxy also means a less frequent need for repairs or replacement, often lasting 10 to 20 years or more with proper care.
Hardwood Flooring
Hardwood flooring costs more upfront, ranging from $6 to $22 per square foot, based on the type of wood and finish selected. Maintenance costs can add up due to the need for special cleaning agents, periodic refinishing, and susceptibility to damage.
Refinishing can cost between $3 and $8 per square foot, and it’s recommended every 7 to 10 years for residential spaces, or more frequently in high-traffic commercial spaces. Despite the higher ongoing care costs, hardwood can last for decades, even a century, with proper maintenance.
Carpet
Carpet is often the cheapest option upfront, with costs ranging from $1 to $5 per square foot depending on the quality and type of material. However, it requires more frequent cleaning, which can include both regular vacuuming and annual deep cleanings by professionals. This typically costs between $0.15 and $0.50 per square foot per cleaning.
Carpets may also need to be replaced every 5 to 15 years, depending on the quality and traffic levels, making them potentially more expensive over the long term than the initial savings might suggest.
Comparing Epoxy Flooring to Tile
Tile flooring offers a wide range of options in terms of materials, colors, and patterns, including ceramic, porcelain, and stone tiles. The cost of tile flooring can vary significantly, ranging from as low as $1 to $15 per square foot, heavily influenced by the type of tile chosen. Floor tiles are well-appreciated for their water resistance and ease of maintenance, making them ideal for bathrooms and kitchens.
Unlike epoxy, tiles can be easily replaced if damaged. They also offer better potential for customization in aesthetic terms. However, the grout lines in tile flooring require regular cleaning to prevent mold and mildew, and the surface can be slippery when wet unless textured treatments are applied.
The choice between epoxy and tile flooring depends on the specific needs, budget, and style preferences of the property owner.
Epoxy vs. Laminate Floors: Which is More Cost-Effective?
Laminate flooring offers a cost-effective alternative with a shorter installation time. It is composed of multiple layers—a core layer of dense fiberboard topped with a photographic image layer and a clear protective layer. While not as durable as epoxy, laminate can last between 15 to 25 years if well-maintained. It is resistant to scratches and easy to clean, making it suitable for areas with moderate foot traffic, like living rooms and offices. The cost of laminate flooring typically ranges from $1 to $5 per square foot, making it a more budget-friendly option upfront.
In terms of cost-effectiveness, laminate flooring is more economical initially due to its lower installation costs and minimal preparation requirements. However, epoxy flooring might be more cost-effective over time, particularly in environments that demand a tougher, longer-lasting surface. The choice between epoxy and laminate flooring ultimately depends on the specific needs of the space, including traffic levels, moisture exposure, and budget constraints.
Is Epoxy Flooring Worth the Investment?
Epoxy flooring is often considered a smart investment for residential and commercial properties. This type of flooring is known for its resilience, ease of maintenance, and can withstand heavy foot traffic. Thus, making it an excellent choice for anyone looking to upgrade their floor system.
Apex Flooring in Florida specializes in epoxy floor installations. They provide services that are not only reliable but also tailored to meet the unique needs of each space. Whether it’s a garage, a warehouse, or a stylish living room, epoxy floors offer a versatile solution that enhances both functionality and aesthetics.
For those considering epoxy floors, Apex Flooring offers a free consultation and quote. This no-obligation service allows potential customers to explore various attractive options and understand the long-term benefits of investing in epoxy flooring.
Don’t hesitate to reach out to Apex Flooring to schedule your free consultation and receive a quote today. Transform your space with a flooring option that combines beauty with resilience.
FAQs
The cost of epoxy flooring ranges from $3 to $12 per square foot, depending on the complexity of the design and the condition of the existing floor. This is relatively economical when compared to hardwood flooring, which can range from $6 to $22 per square foot. Epoxy flooring is generally considered cost-effective than other high-end flooring solutions like hardwood or marble.
Absolutely! Epoxy floors can increase home value, particularly in spaces like garages, basements, and utility areas where durability and maintenance are significant concerns. By providing a glossy finish that provides resistance to stains and wear, epoxy floors make these areas more appealing to potential buyers, potentially increasing the property’s overall marketability.
Yes, epoxy floors are worth the investment for many homeowners. This is because of their longevity, resistance to damage, and low maintenance needs. They are particularly valuable in areas of high traffic or where chemical spills are possible, as they withstand harsh conditions without deteriorating. Additionally, their aesthetic appeal can be customized to fit various decors, making them a versatile choice for both residential and commercial applications.
Epoxy and polyurethane are both types of synthetic resins used in floor coatings, but they differ significantly in their properties and applications. Epoxy is renowned for its strength, bonding capabilities, and durability, making it ideal for heavy-duty industrial environments. Polyurethane, on the other hand, is more flexible and resistant to UV radiation, making it better for areas exposed to sunlight. It also has a higher resistance to scratches and impacts, which can be advantageous in commercial settings.
The cost to epoxy a garage floor typically ranges from $1,500 to $3,000 for a standard 2-car garage. This estimate includes surface preparation, the cost of materials, and professional labor. Factors that can affect the cost include the current condition of the concrete floor, the complexity of the color and design chosen, and any necessary repairs or surface preparation required before application.
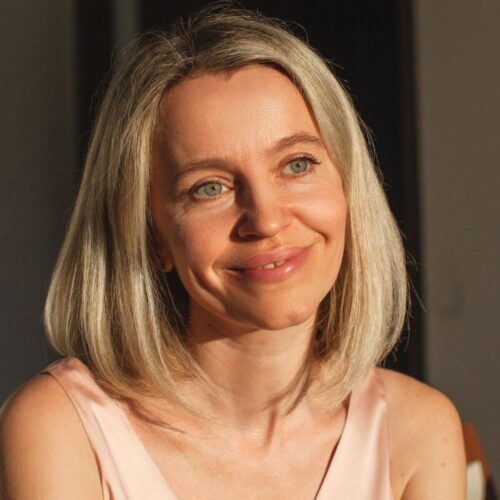
Written By:
Laura Gibson
With a bachelors in creative writing and a passion for home design, Laura Gibson connects the dots between design theory and practical flooring solutions. Her expertise is particularly valuable in discussions about how epoxy flooring fits into contemporary interior design trends, providing readers with a blend of practical advice and design inspiration.
Table of Contents
Related Epoxy Flooring News
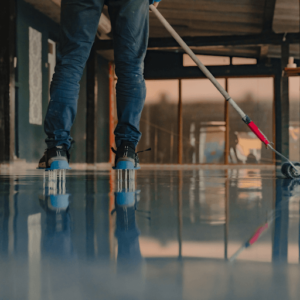
How Epoxy Flooring Meets the Unique Demands of Florida Warehouses
Transform your home with a durable epoxy resin garage floor in just one day. Follow
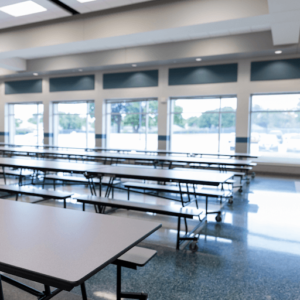
How Epoxy Flooring Can Improve Hygiene in Florida School Cafeterias
Transform your home with a durable epoxy resin garage floor in just one day. Follow
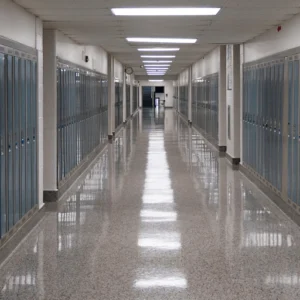
Why Epoxy Flooring Is a Game Changer for School Safety in Florida
Transform your home with a durable epoxy resin garage floor in just one day. Follow
Get In Touch
Get a Free Epoxy Flooring Estimate
